"Smart transformation and digital transformation" is an important measure and way to create and build a modern industrial system. As a manufacturing and smart manufacturing area in Shanghai, how can Jiading fully stimulate the endogenous motivation of enterprises? Recently, the Shanghai Municipal Economic and Information Commission released the "Notice on the List of Municipal Smart Factories to be Selected in 2023", and 15 enterprises in Jiading District were listed. Shanghai Liancheng (Group) Co., Ltd. - "Smart Complete Water Supply Equipment Smart Factory" was honored to be selected.
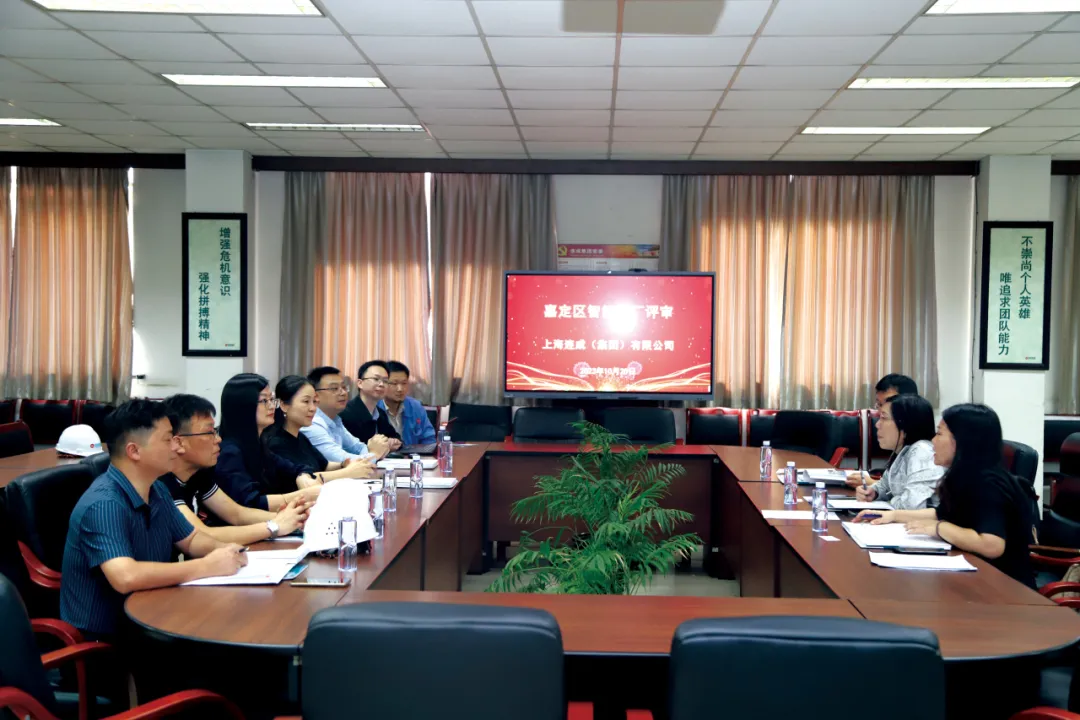
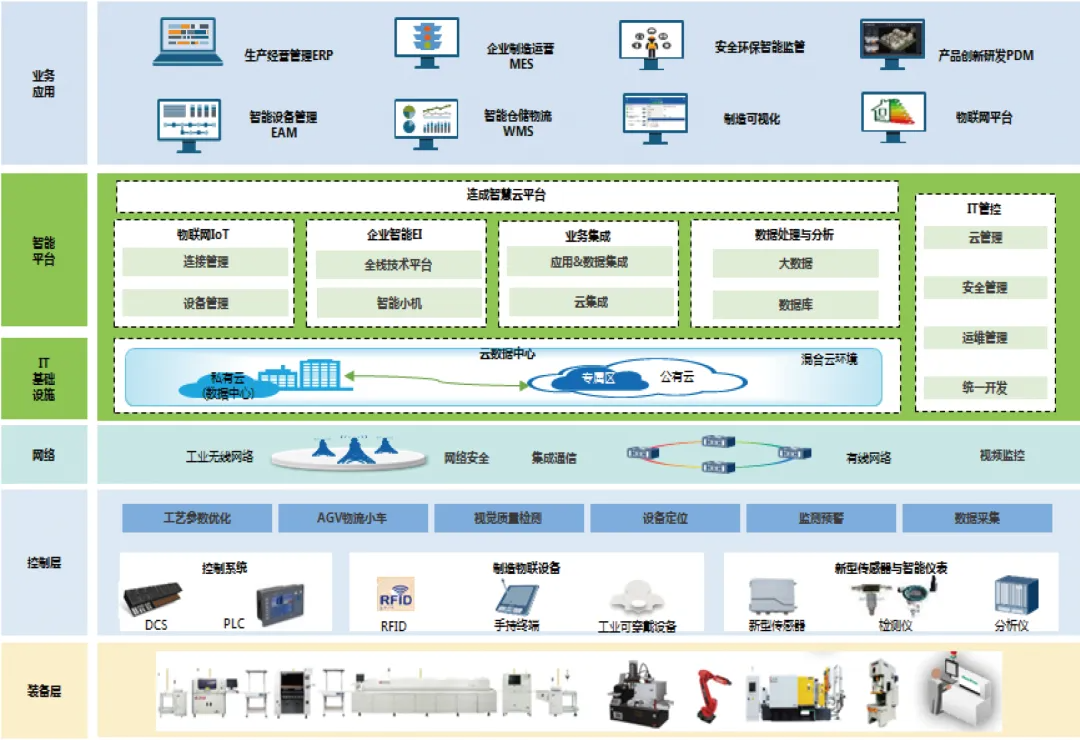
Smart factory architecture
Liancheng Group integrates the business application layer, platform layer, network layer, control layer, and infrastructure layer through the Internet of Things and digital technology, breaking through the information barriers between the management system and automation equipment. It organically combines OT, IT, and DT technologies, highly integrates various information systems, realizes the digitization of the entire process from operation to manufacturing production, improves the manufacturing process, increases the flexibility of the manufacturing process and the controllability of the processing process, and uses networked collaborative management to realize the digital smart factory production model of "intelligent control, data platformization, information integration, and transparent visualization".
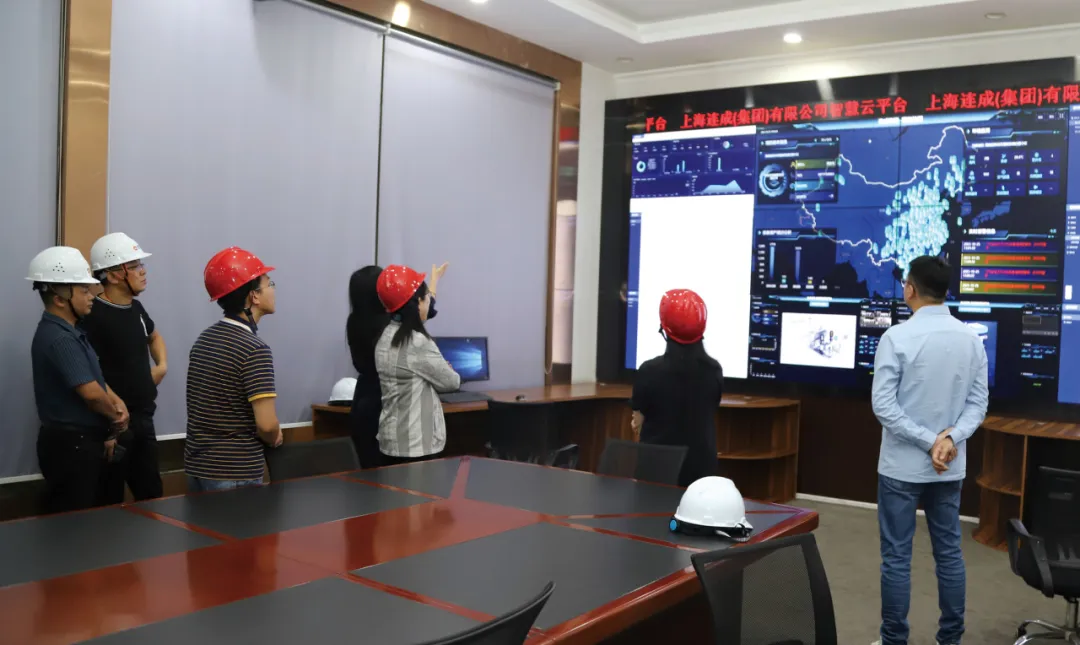
Smart cloud platform network integration architecture
Through the edge acquisition terminal developed by Liancheng and Telecom, the PLC master control of the complete set of water supply equipment is connected to collect the start and stop status, liquid level data, solenoid valve feedback, flow data, etc. of the complete set of equipment, and the data is sent to the Liancheng smart cloud platform through 4G, wired or WiFi networking. Each configuration software obtains data from the smart cloud platform to realize digital twin monitoring of pumps and valves.
System architecture
Fenxiang Sales is used in sales applications across the country to manage customers and business leads, and sales order data is aggregated into CRM and transferred to ERP. In ERP, a rough production plan is formed based on sales orders, trial orders, inventory preparation and other needs, which is corrected through manual scheduling and imported into the MES system. The workshop prints the material delivery order in the WMS system and hands it over to the worker to go to the warehouse to pick up the materials. The warehouse keeper checks the material delivery order and writes it off. The MES system manages the on-site operation process, production progress, abnormal information, etc. After production is completed, storage is carried out, and the sales issue a delivery order, and the warehouse ships the products.
Information construction
Through the edge acquisition terminal developed by Liancheng and Telecom, the PLC master control of the complete set of water supply equipment is connected to collect the start and stop status, liquid level data, solenoid valve feedback, flow data, etc. of the complete set of equipment, and the data is sent to the Liancheng smart cloud platform through 4G, wired or WiFi networking. Each configuration software obtains data from the smart cloud platform to realize the digital twin monitoring of pumps and valves.
Digital lean production management
Relying on the MES manufacturing execution system, the company integrates QR codes, big data and other technologies to carry out precise dispatching based on resource matching and performance optimization, and realize the dynamic configuration of manufacturing resources such as manpower, equipment, and materials. Through the big data analysis, lean modeling and visualization technology of the digital lean production platform, the information transparency between managers, employees, suppliers and customers is improved.
Application of intelligent equipment
The company has built a national "first-class" water pump testing center, equipped with more than 2,000 sets of advanced production and testing equipment such as horizontal machining centers, laser rapid prototyping machines, CNC vertical lathes, vertical CNC turning centers, CNC horizontal double-sided boring machines, CNC pentahedron gantry milling machines, gantry moving beam milling machines, gantry machining centers, universal grinders, CNC automation lines, laser pipe cutting machines, three-coordinate measuring machines, dynamic and static balance measuring machines, portable spectrometers, and CNC machine tool clusters.
Remote operation and maintenance of products
The "Liancheng Smart Cloud Platform" has been established, integrating intelligent sensing, big data and 5G technologies to achieve remote operation and maintenance, health monitoring and predictive maintenance of secondary water supply pump rooms, water pumps and other products based on operating data. The Liancheng Smart Cloud Platform consists of data acquisition terminals (5G IoT boxes), private clouds (data servers) and cloud configuration software. The data acquisition box can monitor the complete equipment in the pump room, the pump room environment, the indoor temperature and humidity, the start and stop of the exhaust fan, the linkage of the electric valve, the start and stop status of the disinfection equipment, the flow detection of the water inlet main, the water tank water level flooding prevention device, the sump water level and other signals. It can continuously measure and monitor the process parameters related to safety, such as water leakage, oil leakage, winding temperature, bearing temperature, bearing vibration, etc. It can also collect parameters such as the voltage, current, and power of the water pump, and upload them to the smart cloud platform to realize remote monitoring and operation and maintenance.
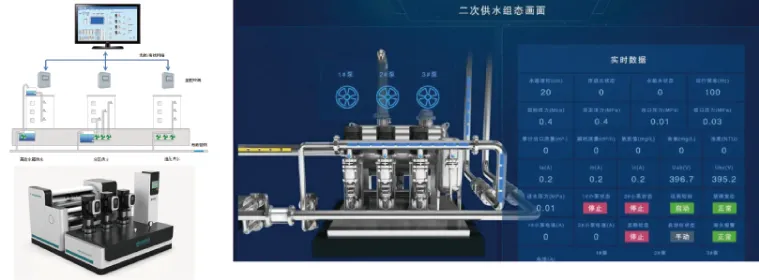
Liancheng Group said that as an important force in promoting the innovation and development of the intelligent industry, the group company is actively participating in this transformation. In the future, Liancheng will unswervingly increase resource investment in R&D innovation and intelligent manufacturing, and optimize the process flow by introducing automated equipment and intelligent control systems, reducing the use of raw materials and energy by 10%, reducing the generation of waste and pollutants, and achieving the goal of green production and low-carbon emissions.
At the same time, through the implementation of the MES manufacturing execution system, using advanced information technology, and comprehensively analyzing materials, production capacity, production site and other constraints, planning feasible material demand plans and production scheduling plans, and achieving an on-time delivery rate of 98%. At the same time, it connects with the ERP system, automatically releases work orders and material online reservations, ensures the balance between product supply and demand and production capacity, reduces material procurement lead time, reduces inventory, increases inventory turnover by 20%, and reduces inventory capital.
Post time: Aug-13-2024